PRP® Industries was founded on the belief that only field-proven corrosion solutions should be brought to market. Only thoroughly field-tested and approved CORSOL® corrosion solutions make it to market, which is why PRP® has the confidence in providing unprecedented corrosion assurance to our Licensed Manufacturing Partners. Many of the original CORSOL® corrosion solutions developed by PRP® now have over 20 years of field success in preventing steel from corroding in the harshest environments throughout the world and are still being used today.
Field-Proven Testing
CORSOL® corrosion solutions are the ONLY long-term, field-proven solutions of their kind, with decades of documented proof. CORSOL® corrosion solution protects the components of over 1 million commercial vehicles in service today.
We seek out equipment being subjected to challenging, brutal usage and environments. Corrosion can have devastating effects on your equipment, requiring refurbishment or replacement. Our mission is to keep your hardworking equipment in the field getting the job done year after year.
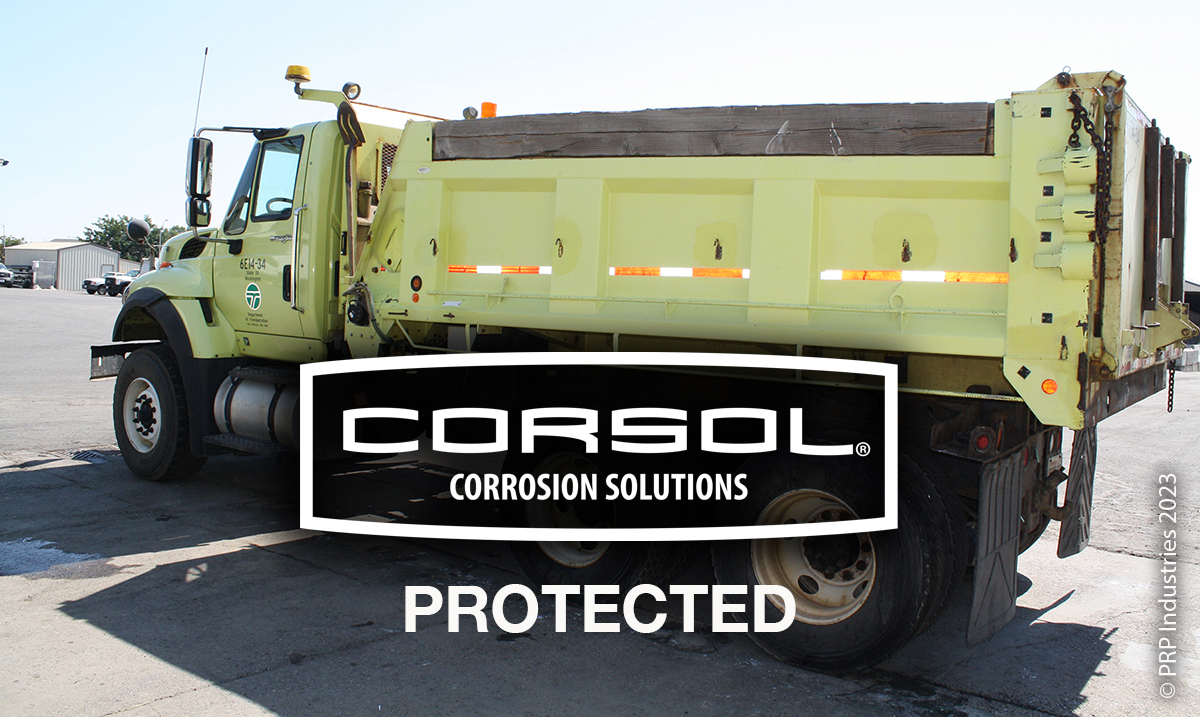
10 years of service – 154,525 miles
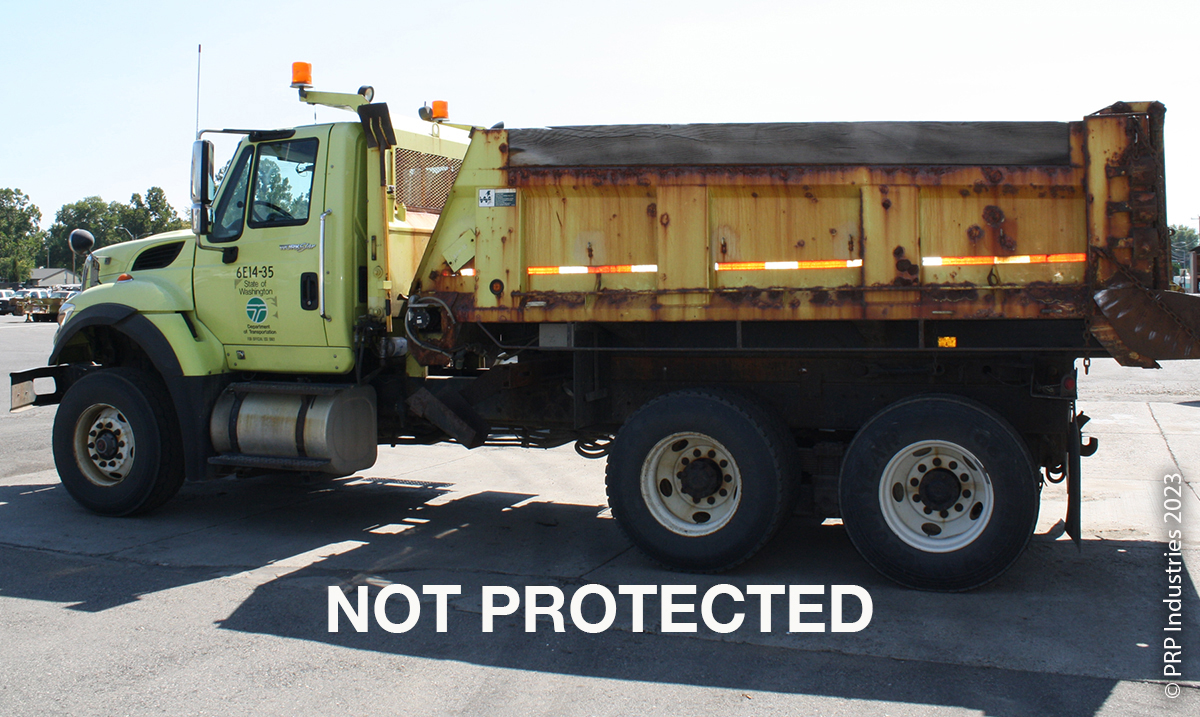
10 years of service – 144,015 miles
ABOVE: Washington State Department of Transportation is particularly hard on its snow removal equipment. Exposure to months of harsh conditions and corrosive road salt while operating in mountainous regions is why we chose their equipment to field test our CORSOL® corrosion solutions. The two salt spreader trucks shown below have continuously operated out of the same facility for ten years.
Rock Chips Corrosion Challenge
Gravel and road debris thrown backward from the tires of equipment vehicles in front of your trailers cause significant rock chips. Due to the high speeds of these stones, they often leave very deep dings in your equipment paint finish, typically on structural underbody components, bumpers, and wheel wells.
The deep dings expose the steel to the elements, which causes oxidation in the metal and forms corrosion. The oxidation process undercuts the primer, separating it from the steel. The undercutting becomes visible once a rock strikes the vulnerable undercut area, causing the paint to flake off. The exposed steel will deteriorate quickly.
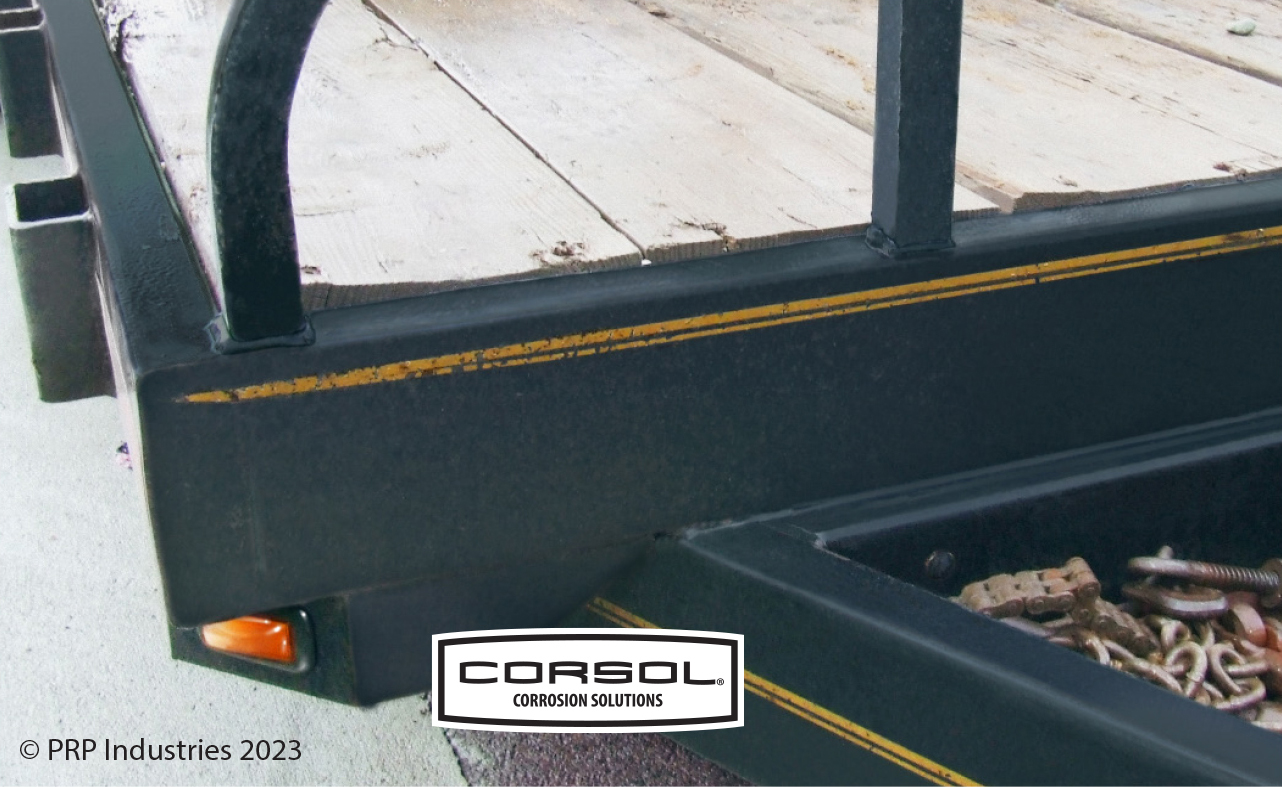
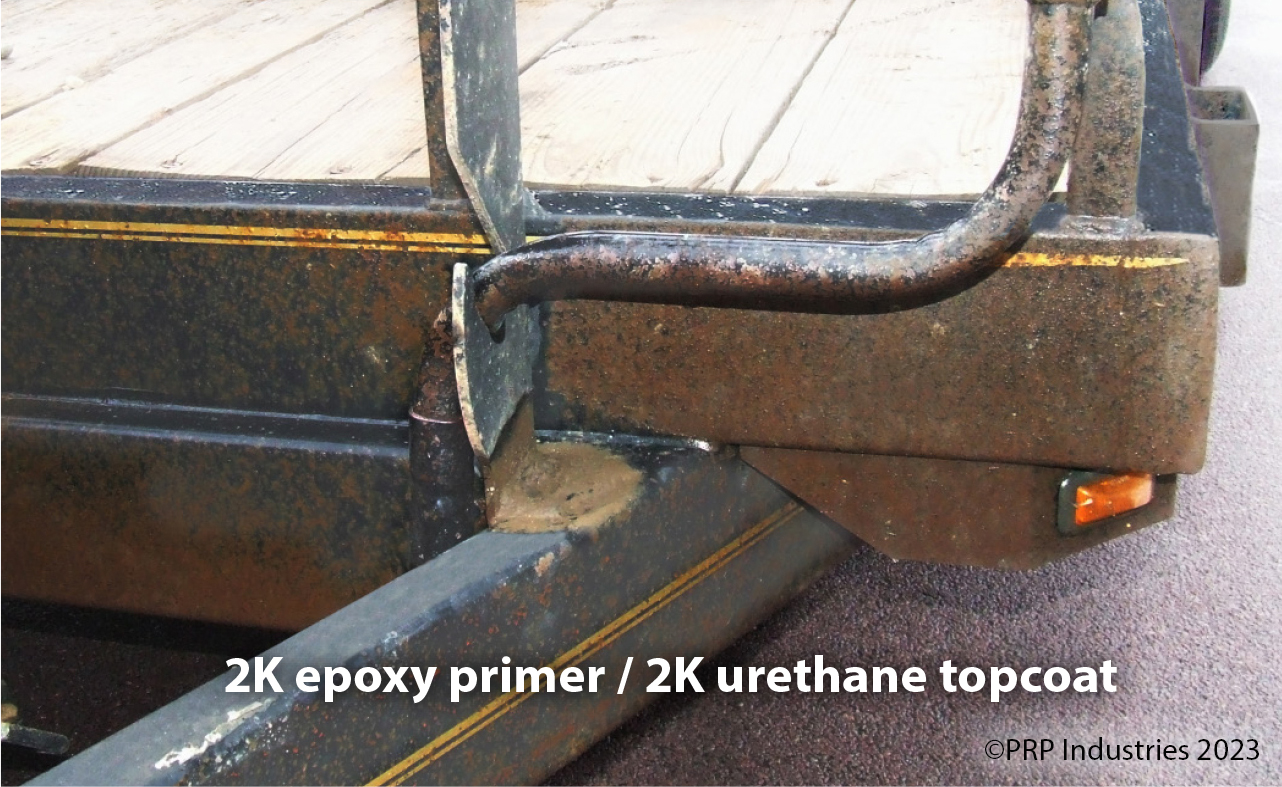
ABOVE: A leading trailer manufacturer performed a rock chip field test. They had a trailer, half protected with CORSOL® corrosion solutions, half painted with 2K epoxy primer/2K urethane topcoat. The trailer’s painted side has substantial undercutting and blistering areas, leading to corrosion flaking and metal deterioration. After three years of service, you can see the CORSOL® corrosion solutions surface rock dings do not undercut and blister, which means your equipment will last longer and look good for years.